
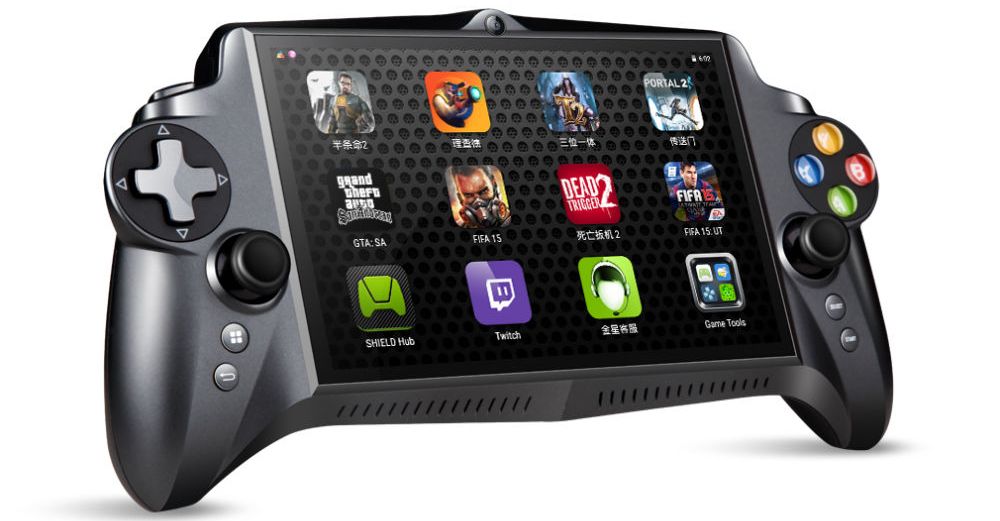
#Best 3d printers 2020 software
Manufacturers either include their own 3D printing program or modify an existing platform such as the open-source Cura.ģD printing software performs three main functions: processing an object file (resizing, moving, rotating, and in some cases duplicating it), slicing it (into virtual layers, based on your chosen resolution), and printing it. Gone are the days when tinkerers had to cobble together several different programs to get a 3D printer to run. What Should I Look for in 3D Printer Software and Connectivity? Still, these very traits should not deter-and may even appeal to-hobbyists and DIY folks.
#Best 3d printers 2020 plus
Some require assembly, being essentially kits, and most require more setup care than a closed-frame printer, plus more maintenance to keep them running smoothly. Open-frames do have some clear downsides by definition: They tend to be noisy, emit odors when certain plastics are melted, and provide little protection for someone who might touch the hot extruder.Īlso, recognize some potential negatives of open frames, depending on the model. If a relatively large build volume is a priority, you’re likely to get more bang for the buck with an open-frame model. Low-cost 3D printers include both open-frame and closed-frame models, as well as a few stereolithography printers. A downside: They tend to have smaller build volumes than open-frame 3D printers, which have fewer (often, no) walls to constrict them. Among their advantages? They muffle the operating noise, as well as reduce the odor from melted filament (which is potentially an issue with ABS plastic), and they provide some protection for people or pets who might inadvertently touch the hot extruder. Closed-frame 3D printers are boxlike devices, with a rigid base, walls (with a see-through door in front), and top. Which brings us to the frame "form factor" question: open-frame versus closed-frame. Should I Get an Open-Frame or Closed-Frame 3D Printer?
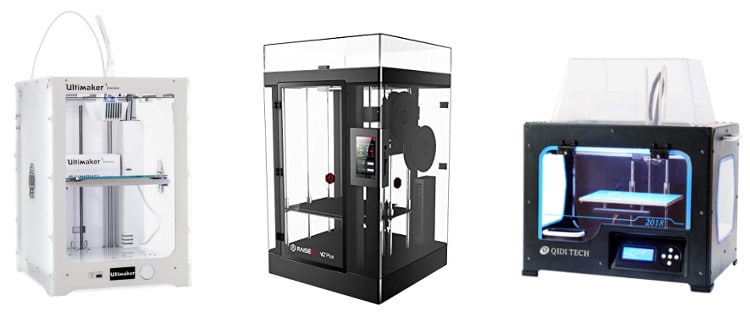
You'll want to weigh the build volume against the kinds of objects you will print. Closed-frame 3D printers-and most semi-open models, which have a rigid top, base, and sides but are open in front and, often, back-tend to have small build volumes, while open-frame printers, lacking as rigid a physical structure, often have relatively large build volumes for the price. This depends in part on the type of printer. (We say “a part” because a 3D-printed object can consist of multiple parts that are printed, then glued or otherwise pieced together.) While the smallest build volume of any 3D printer we have tested is 3.9 by 3.9 by 4.9 inches, we consider any build volume smaller than 6 by 6 by 6 inches to be small, any between that and 10 by 10 by 10 inches as medium, and any printer with at least one build dimension of more than 10 inches as having a large build volume.Īs a general rule, inexpensive 3D printers have small build volumes, while more expensive ones have larger build volumes. What's the Right Build Volume for a 3D Printer?Ī 3D printer’s build volume is the maximum dimensions (HWD) of a part that it can print. These include the build volume, the type of frame, the varieties of supported filament, the software, and the connectivity mix. What separates more expensive 3D printers from cheap ones ("cheap" defined as $500 or less, for the purposes of this article) is often a select group of features. Most 3D printer manufacturers have either developed and refined their own software, or have adapted an open-source printing platform such as Cura. Automatic print-bed leveling is the norm, and you can usually remove 3D-printed objects from heated and/or flexible build plates with a minimum of coaxing. Nowadays, many of those ornery 3D-printing issues have been resolved (most of the time, anyway), even for consumer and bargain-priced 3D printers.
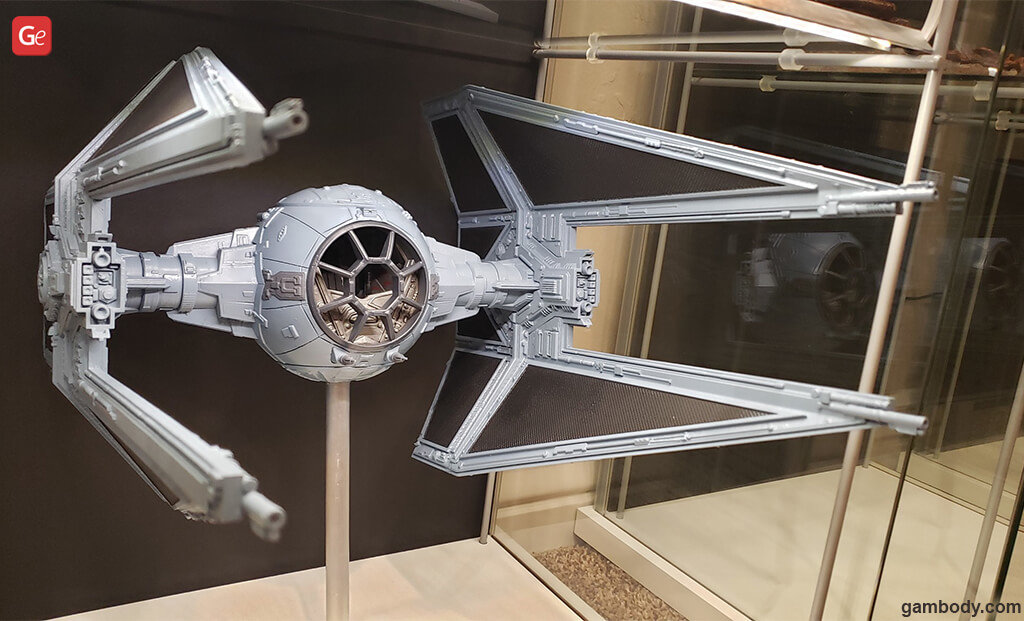
The big difference is the change that has come to the cheaper models. While they can still be rebellious at times, 3D printers have grown up a lot, and achieving the 3D printer basics has gotten a lot less likely to end in a shouting match over small things. These and other issues required painstaking effort to resolve, often combined with calls to tech support.

Objects frequently stuck to the build plate, and required careful, sometimes unsuccessful, efforts to pry them off. The extruder or hot end had to be positioned just right to minimize the gap between the nozzle and the build plate (the flat surface on which the object is printed). Filament feeders had to be coaxed into delivering filament from the spool to the extruder.
